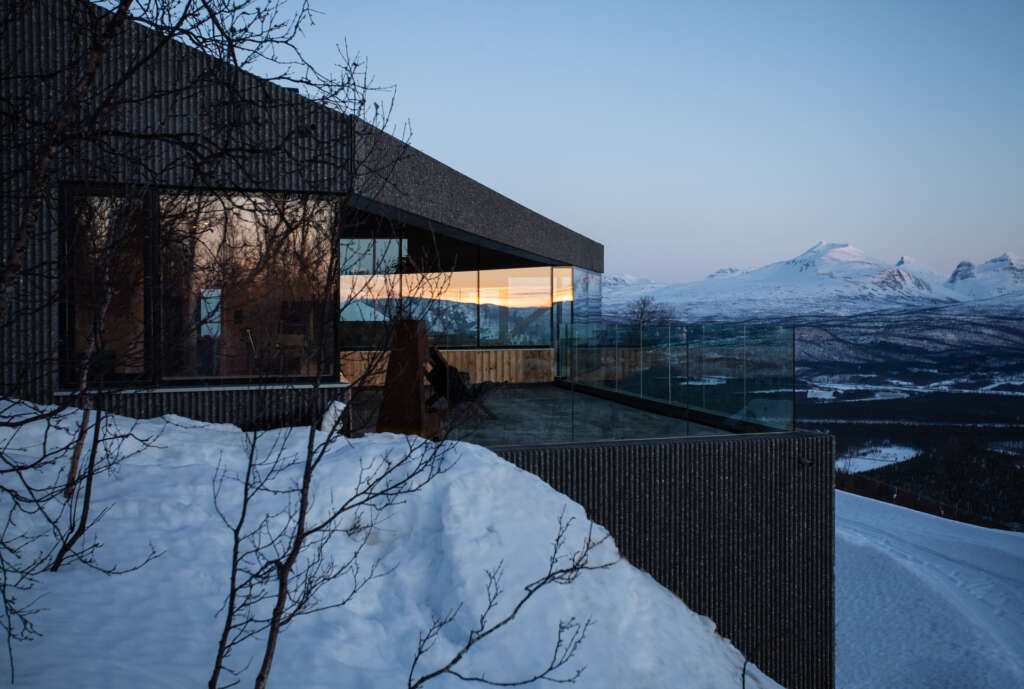
Concrete Cabin
Architect: Hamran/Johansen Arkitekter AS (HAJA)
Location: Norway
Type: Cabin
Year: 2021
Photographs: courtesy of HAJA
The following description is courtesy of the architects. The concrete cabin is located on a steep slope directly adjacent to the ski resort. The southern part of the site has been relocated in connection with the establishment of the alpine facility, so that it is less problematic to do excavation. The northern part of the plot has a natural character with heather grabs and mountain vegetation that is taken care of as much as possible. The house is closed to the mountain and the access side, and opens onto the view. The roof is triangulated folds, which reach almost down to the terrain at the rear edge. The roof is covered with peat, so that the building appears as an abstract extension of the landscape. The entrance level contains a
spacious entrance hall, living room / kitchen, and master bedroom and bathroom. Downstairs contains the other three bedrooms, a separate living room and bathroom with sauna. The steps protrude elegantly, with a thickness of 40mm. This is made possible by the use of fiber-reinforced concrete.
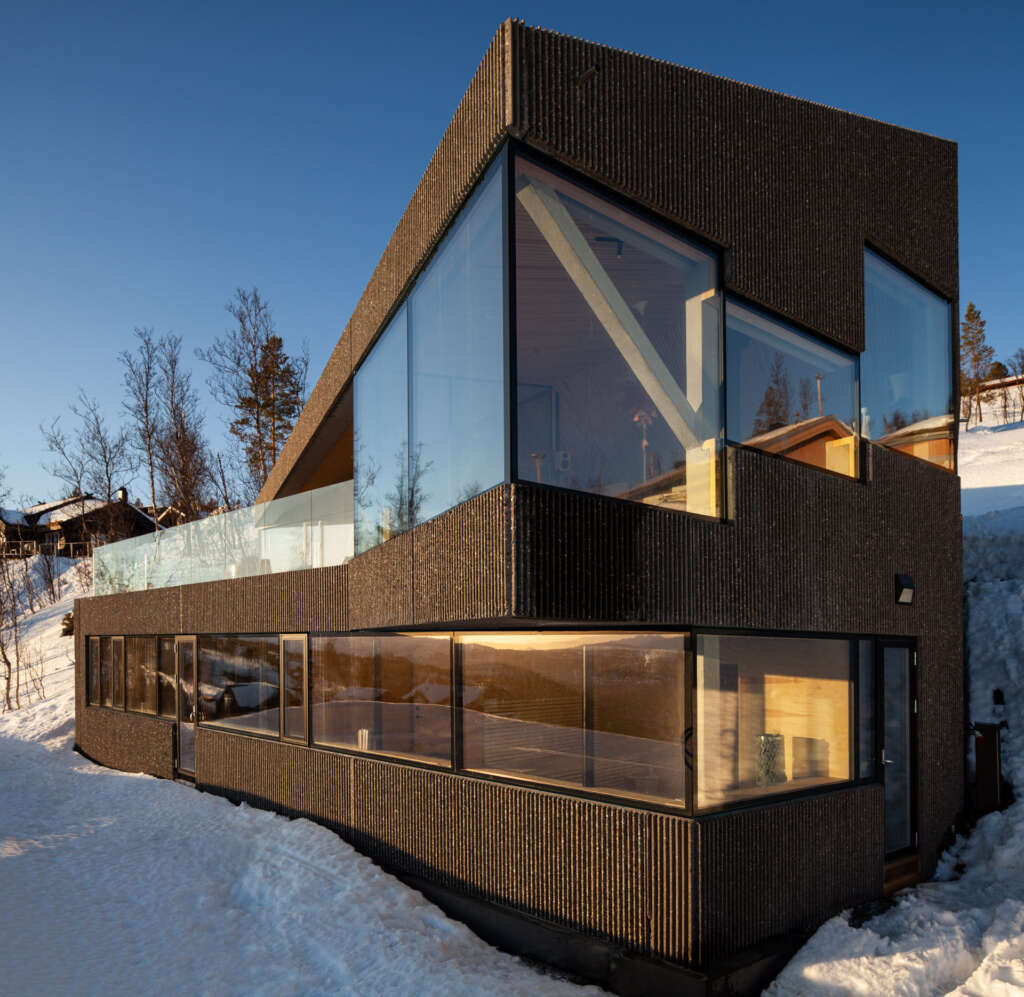
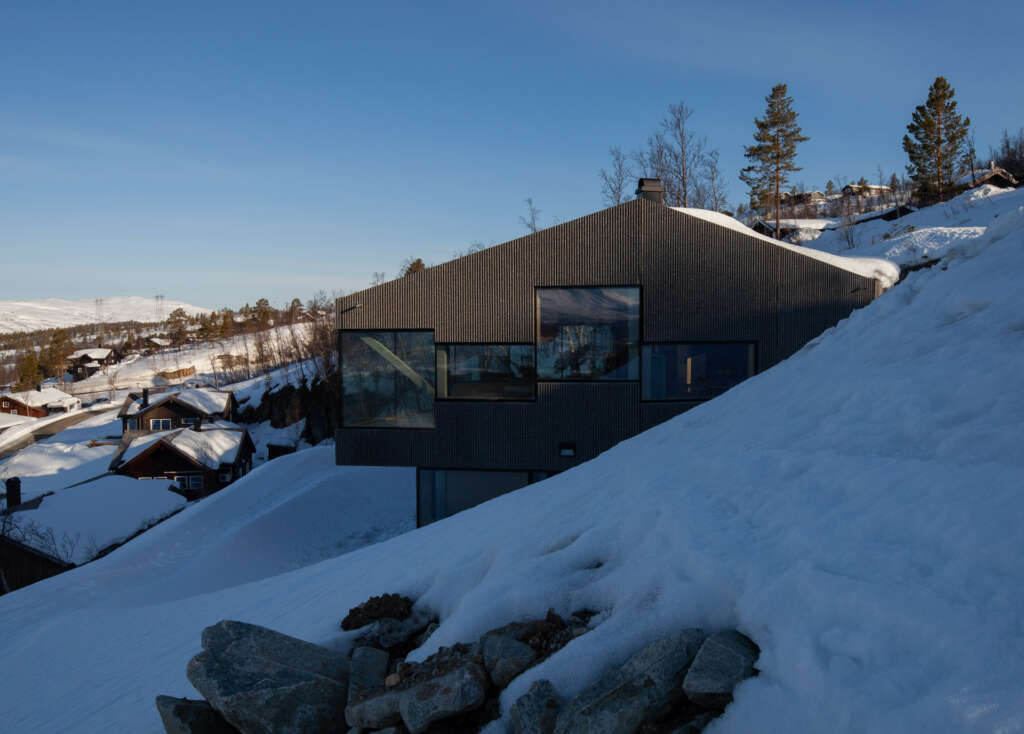
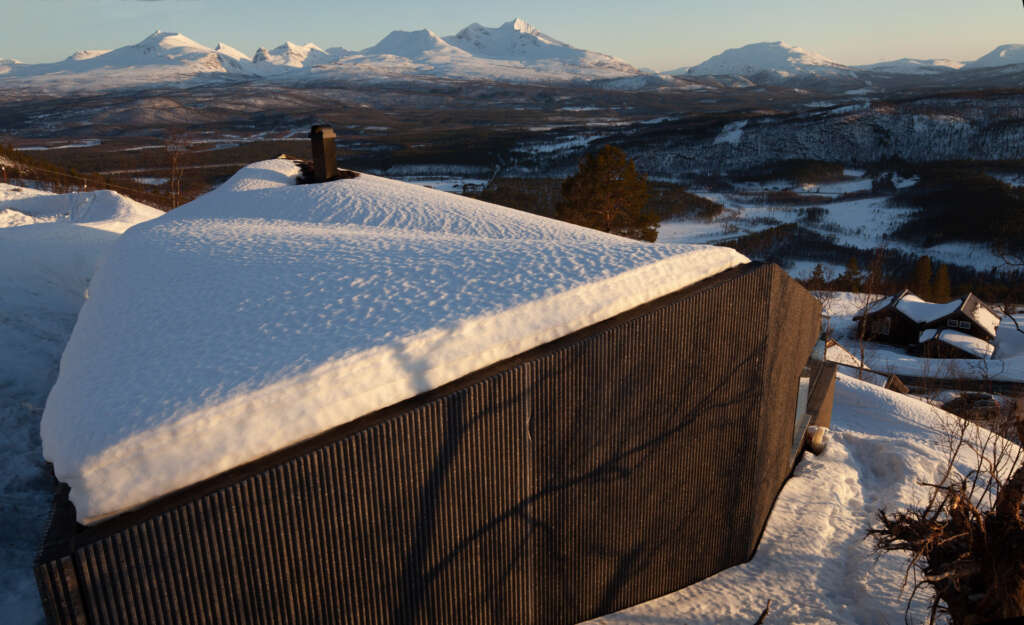
The choice of material is strongly connected to the plot and the context. Concrete is an inorganic material, but at the same time full of life. Concrete is, architecturally speaking, a natural material. Especially when local aggregate is exposed in the facade. The raw concrete therefore forms an ideal framework for contemporary rooms in the mountain landscape. The concrete will be affected by weather and wind, and over time will appear more and more as an integral part of the landscape. The wall of the sheds is clad with recycled formwork plank, which creates a beautiful surface and a relationship to the concrete surfaces. The main materials inside are concrete, glass and pine. All surfaces are untreated. The inside of the outer walls has retained its surface in concrete, while the light walls, floor and ceiling are untreated pine. The wood contributes to the feeling of warmth, and improved acoustics. Concrete, glass and wood have been installed with very high precision, a prerequisite for a successful result.
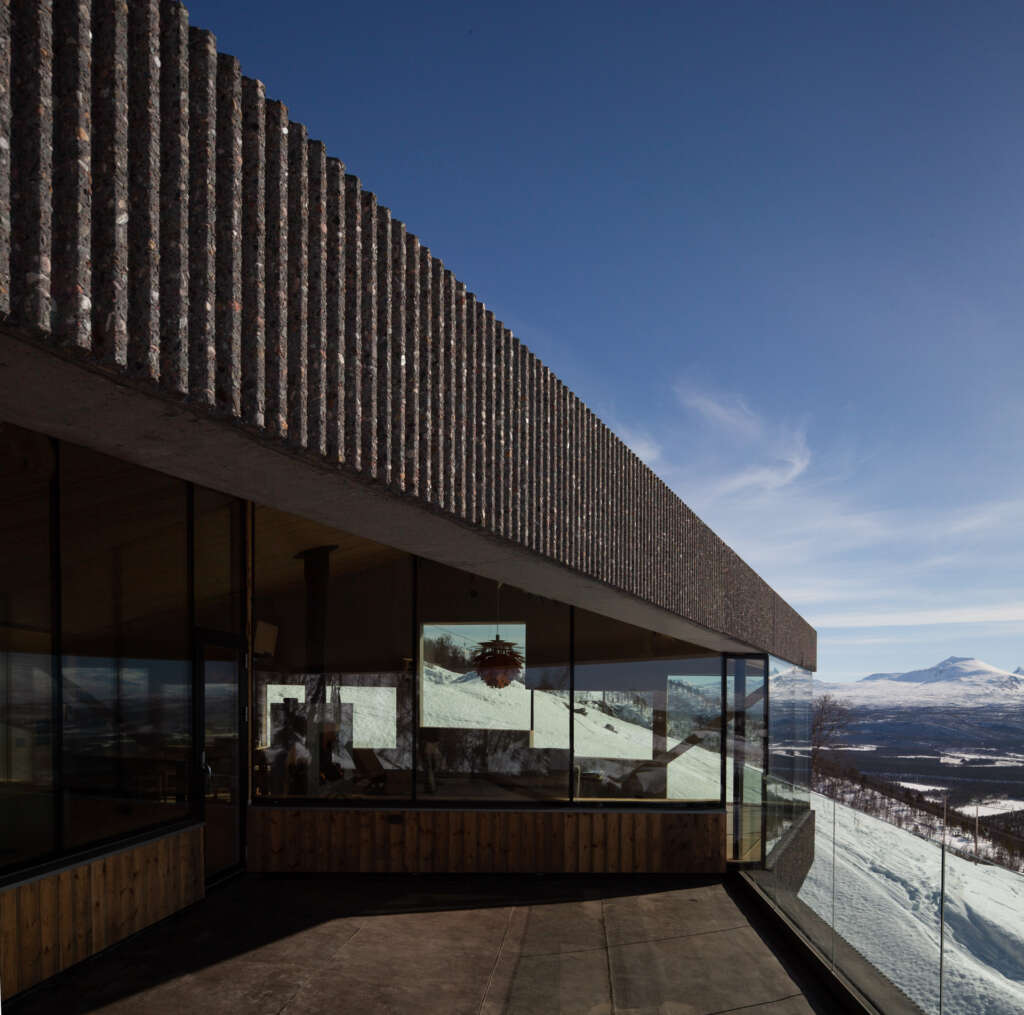
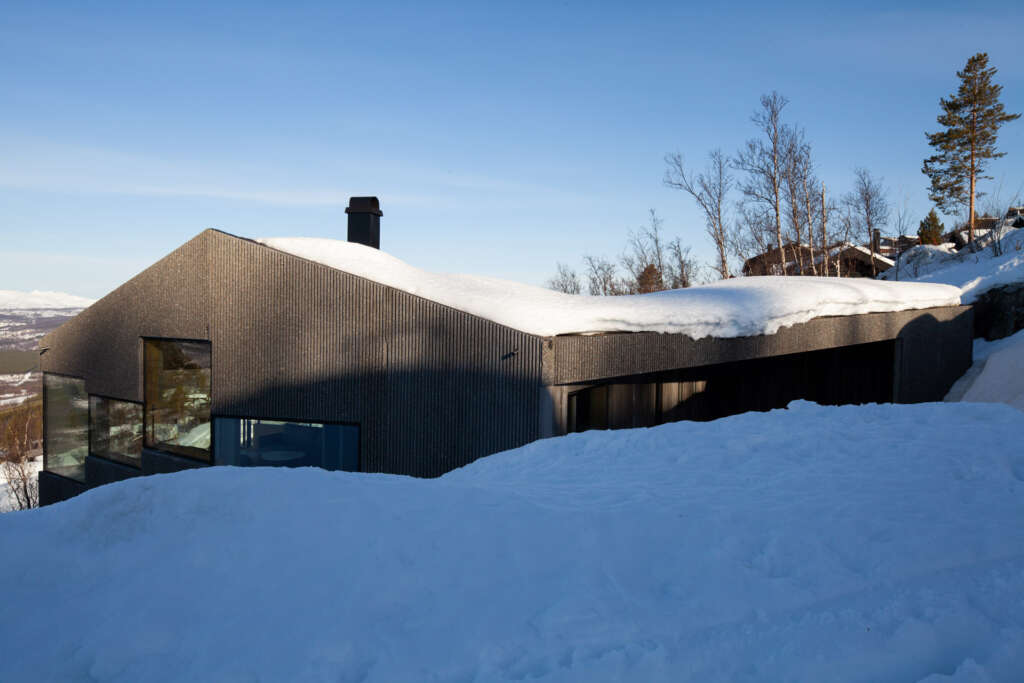
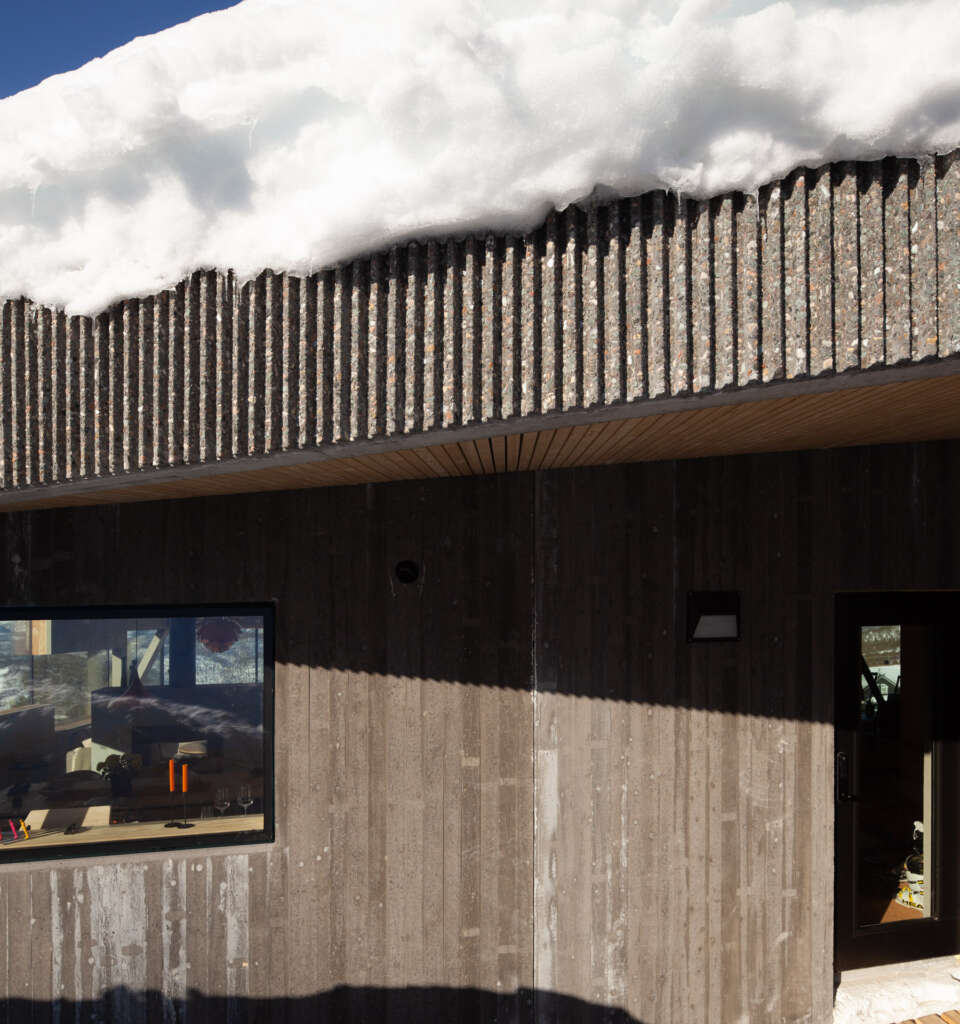

The use of elements enables production, even when the temperature is below the limit for space casting. Prefabrication also provides a significant cost reduction. In the outer walls we have used hand-carved matrix, specially designed by the architect, which creates a deep relief. The elements are planned so that there are no horizontal joints between the elements. That way we avoid breaks in the texture. All vertical joints between the elements are planned so that they lie between the grooves and after grouting are barely visible. In this way, the monolithic character of the house is substantiated. The aggregate is charged, local moraine stone from Målselv, which is exposed in the facade. The concrete in the outer layer is slightly pigmented black to achieve a hue that hits the mountain landscape in the best possible way. Inside, the concrete is exposed. The building has continuous window bands which appear unbroken in the façade. In the south façade, there are continuous elements where the inner beams are reduced to individual columns. Along the west façade come the elements in the form of long beams, subdivided by steel columns. The glass is glued into the construction without the use of visible frames. The distinction between outside and inside is minimized, and the experience of being in the mountain landscape is enhanced.
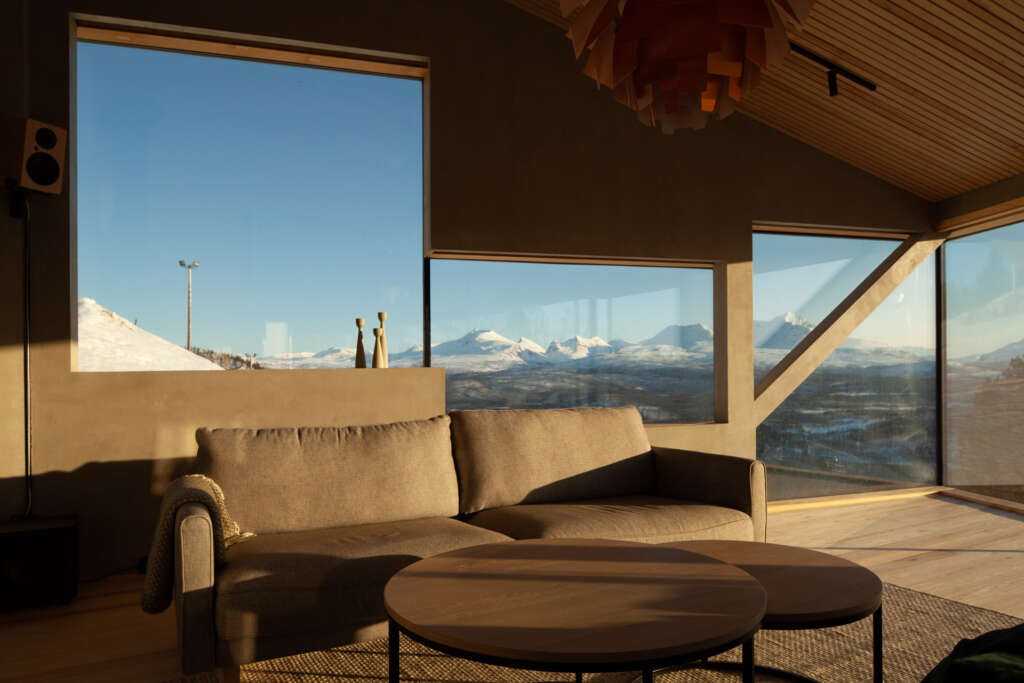
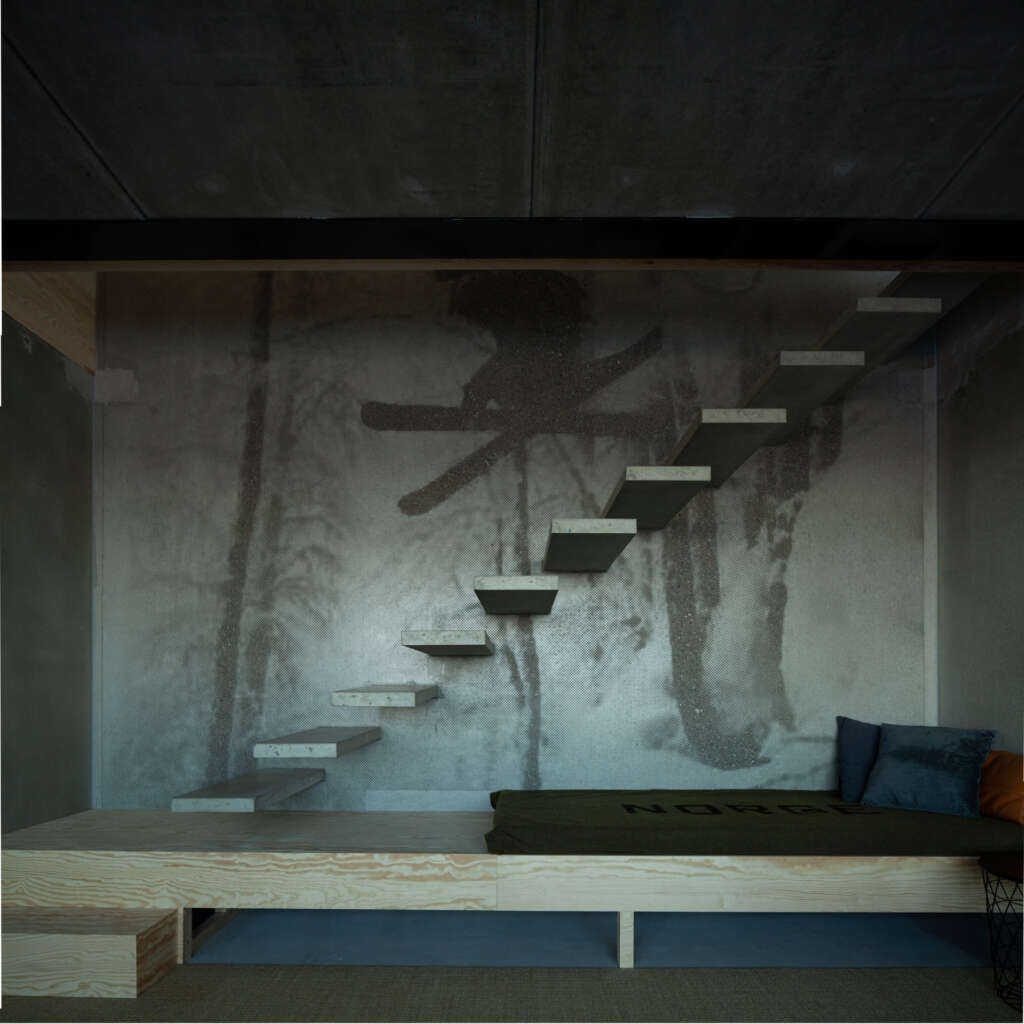
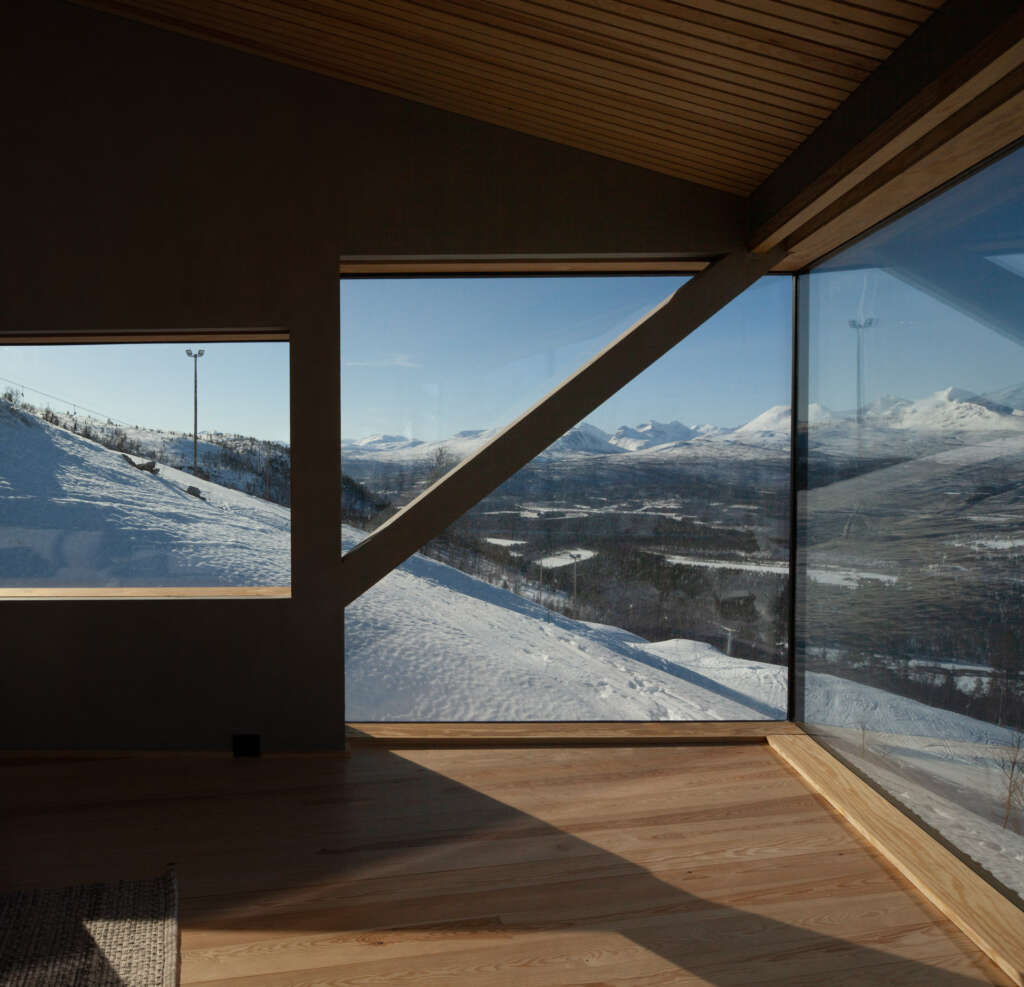
The project goes a long way in exploring the architectural potential of the concrete element. In terms of production technology, the project has been challenging, especially considering the complexity of geometry. The design is done with innovative use of BIM technology and detailed 3D models where all construction parts have been accurately planned. There has been a continuous and close collaboration with the engineer and element manufacturer during the planning. The close collaboration, and the willingness to pull in the same direction has been crucial for the quality. The concrete cabin demonstrates a potential for more extensive use of prefabricated concrete in architecturally demanding projects. The concrete is produced at the factory, one hour’s drive from the site. Local aggregates and craftsmen from the surrounding area have been used. This contributes to local value creation, and the short-distance aspect
contributes to a very sustainable environmental perspective.
The project is the result of a bold process and a very good collaboration between architect, client and element manufacturer.
Lars Hamran/Primary Architect